The new structure of the tap
The new structure of the tap
Modern faucets have a variety of new structures to improve the cutting efficiency of taps, improve chip holding and chip removal, and reduce tooth chipping and breakage.
1. Spiral point tap: The cutting part is ground with a chute to form a negative blade inclination angle (see tool), and the chips are discharged forward during cutting, which is suitable for processing through holes.
2. Spiral flute tap: The chip flute is helical. When processing right-handed thread in a blind hole, the fixture should make a right-hand spiral chip flute so that chips can be discharged forward without scratching the line.
3. Slotless Extrusion Tap: The thread is formed by the plastic deformation of the metal when the hole wall is extruded. It is mainly used for processing plastic materials such as aluminum alloy and copper and can also process low-carbon steel and stainless steel. The extruded taper at the tip of the tap is a tapered thread. To reduce friction and extrusion force, the section of the fixture is made into a polygon. The extrusion tap has high strength and is especially suitable for processing small-sized screw holes with a diameter of less than 6 mm.
4. Jumping tooth tap: Grind one tooth alternately along the winding direction of the cutter tooth, thus increasing the chip thickness, which is beneficial to chip breaking and chip removal and is used for processing stainless steel and other workpieces.
5. Internal chip tap: chips are discharged from the inner hole of the fixture, which is used to process large-sized screw holes.
6. Automatic retraction tap: After the tapping is completed, the cutter teeth of the fixture can automatically shrink inward for quick withdrawal.
7. Broaching tap: A broach with teeth distributed on the helix, often used to process trapezoidal and square threads.
8. Carbide taps: mainly used for processing cast iron and non-ferrous metals, with high cutting efficiency and tool life.
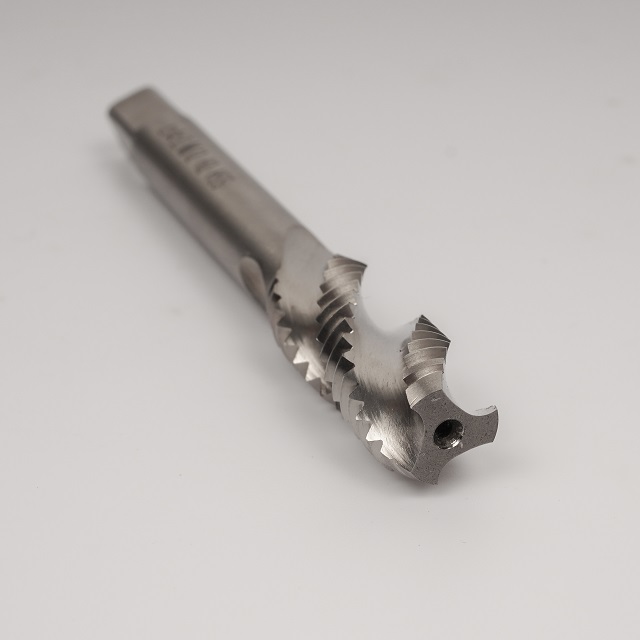
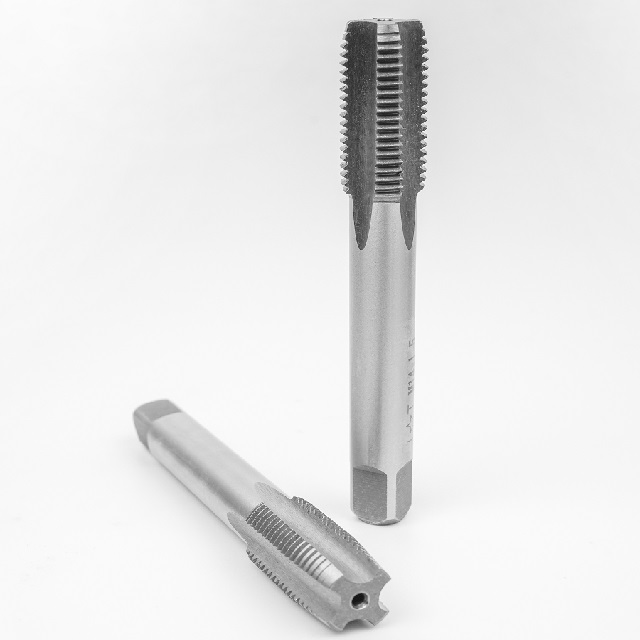
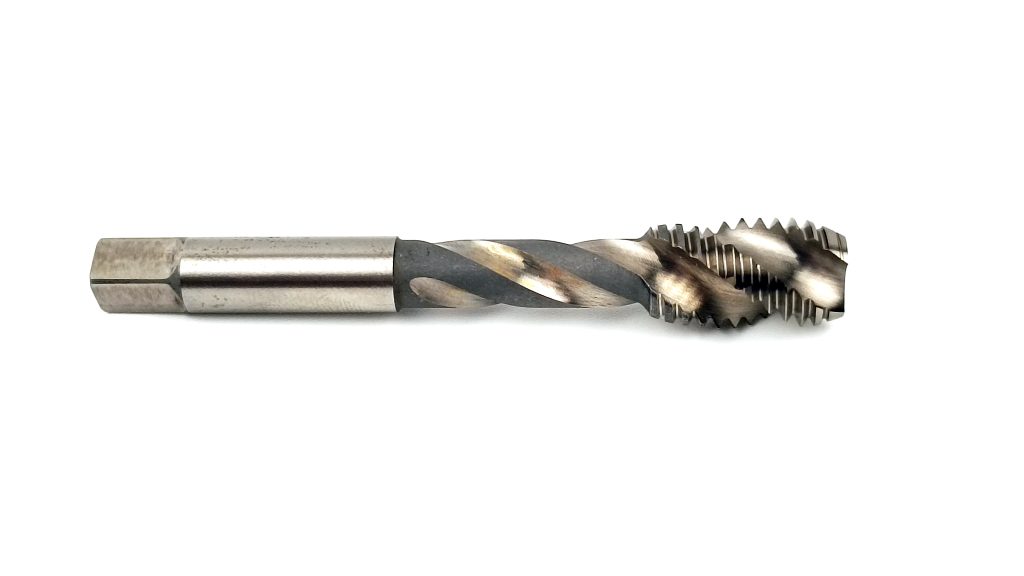