Several types of tap die
Several types of tap die
Tap classification
1. According to different drivers: hand taps and machine taps
2. According to the processing method: cutting tap and extrusion tap
3. According to the thread to be processed: metric coarse thread taps, metric fine thread taps, pipe thread taps, etc.
4. According to its shape, it is divided into straight flute taps, spiral flute taps, and spiral point taps.
5. According to the tapping direction of the taps, they can be divided into straight and reverse taps.
Straight flute tap
Straight flute taps have the best versatility and the strongest rigidity. Therefore, straight flute taps are generally preferred when processing materials with higher hardness (such as hardened steel above 40HRC) and chips in powder particles (such as cast iron and cast aluminum).
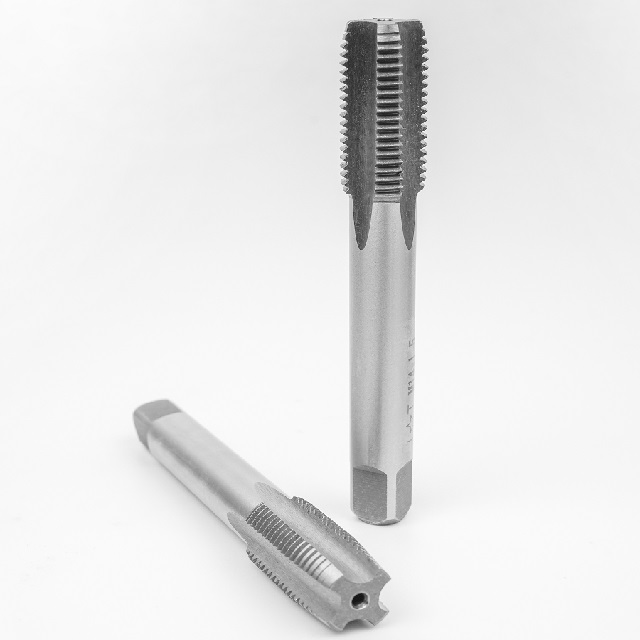
Spiral flute tap
Spiral flute taps are more suitable for processing non-through hole threads (also called blind holes), and chips are discharged upward during processing. Due to the helix angle, the actual cutting rake angle of the tap will increase with the increase of the helix angle. Experience tells us that when processing materials with high hardness, the helix angle should be selected smaller, generally around 30 degrees, to ensure its rigidity and to prolong the life of the tap. When processing non-ferrous metals such as copper, aluminum, magnesium, and zinc, which are not very hard materials, the helix angle should be selected larger, which can be around 45 degrees, and the cutting should be sharper, which is conducive to chip removal.
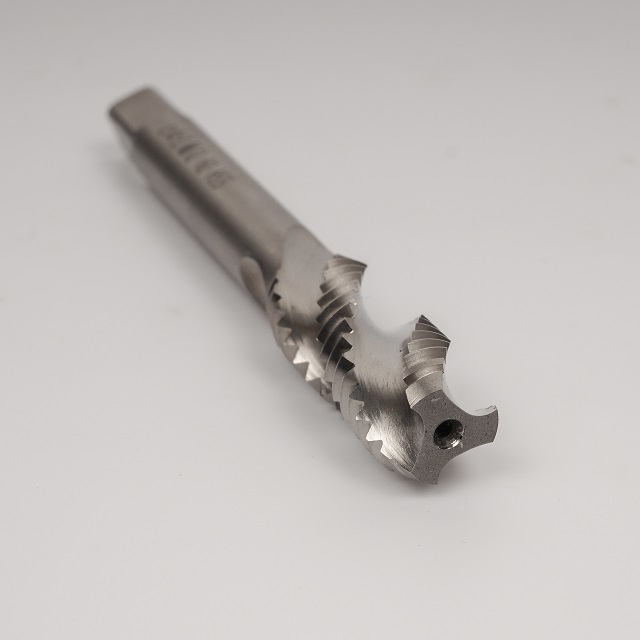
Angle tap
Chips are discharged forward when processing threads and through-hole threads should preferably use edge angle taps. Since its design is based on the straight-fluted tap, a hole is cut obliquely with a grinding wheel at the blade’s tip, so its rigidity is comparable to that of the straight-fluted tap.
extrusion tap
Different from the three types mentioned above of cutting taps, the processing method of the extruding tap is to extrude the shape of the internal thread in the bottom hole by extrusion molding through the plastic deformation of the material itself. Therefore, the processed material should be easy enough. Its advantage is that it does not produce chips, which can eliminate 90% of machining problems. However, because it is extruded, there are fine grooves on the top of the processed internal thread, which is unsuitable for jobs with high airtightness requirements.