Common Tap and die Coating Types
Common Tap and die Coating Types
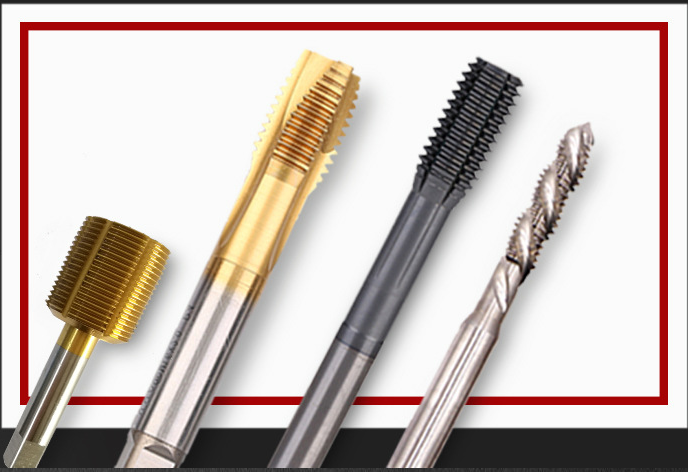
1. Steam oxidation
Steam oxidation treatment is a surface oxidation treatment technology. The tap is in contact with steam at a temperature of 540~560°C. In high-temperature water vapour, a layer of blue oxide film is formed on the surface. This oxide film has a fine structure and can be firm. It is attached to the metal surface.
The tap coating has good adsorption to coolant, good anti-rust performance, and can store oil, play a role of lubrication, reduce friction, reduce friction prevent bonding with the processed material at the same time, and improve the lives of the tap. It is said that the life of tap tools can be increased by at least 20% after steam treatment.
2. Nitriding treatment
Nitriding treatment refers to a chemical heat treatment process in which nitrogen atoms penetrate the surface of the workpiece in a certain medium at a certain temperature. Common nitriding treatment methods include gas nitriding, liquid nitriding and ion nitriding.
The surface of the nitriding-treated tap is nitrided to form a surface-hardened layer, which has excellent wear resistance, fatigue resistance, corrosion resistance and high-temperature resistance.
3. Titanium nitride coating
Titanium nitride coating is a general-purpose PVD coating. It has been a common coating since the invention of PVD technology. It has high-cost performance and is also a widely used PVD coating in the past years. It Has high film hardness.
The appearance of the coating is golden yellow, easy to produce, low in cost, and widely used. Generally, it can increase the life of taps by about 300%. It has good hardness, lubricity, and good Adhesion.
Titanium nitride coating can improve the surface hardness and high-temperature stability of the tap, reduce the friction coefficient of the top surface, and prolong the service life.
4. Titanium carbon nitride coating
Titanium carbon nitride coating is a solid solution coating formed by nesting two face-centred cubic lattices of titanium nitride and carbon nitride. Due to the combination of both advantages, it has high hardness, low friction coefficient and good wear resistance. And other advantages.
The surface of the coating is blue-grey, with a surface hardness of 3000HV, which can withstand high temperatures of 400°C.
5. Titanium aluminium nitride coating
The titanium aluminium nitride coating has a blue-grey appearance, a surface hardness of up to 3400HV, and an oxidation resistance temperature of 900°C. It has good heat insulation, a compact structure, and higher temperature resistance.
After the coating is coated on the surface of the tap, a layer of aluminium oxide film can be formed to improve the high-temperature processing life of the fixture. If the content of aluminium in the coating is further increased, the oxidation resistance of the coating will also be improved accordingly.
6. Chromium nitride coating
Chromium nitride coating is also a kind of PVD coating. Its appearance is silver grey, with high hardness (1800-2000HV), strong corrosion resistance, high-temperature oxidation resistance (700 ° C), good Adhesion, and good lubrication performance, which can prevent Adhesion and sticking phenomena such as plastic injection and die-casting powder sintering.
The main purpose of tap coating
1. Increase the surface hardness and wear resistance of the tap;
2. Reduce the friction between the tap and the workpiece, enhance the smooth extrusion effect, and avoid premature damage to the tap;
3. Improve the surface quality of the workpiece;
- Increase the speed of extrusion and tapping to shorten the processing time.
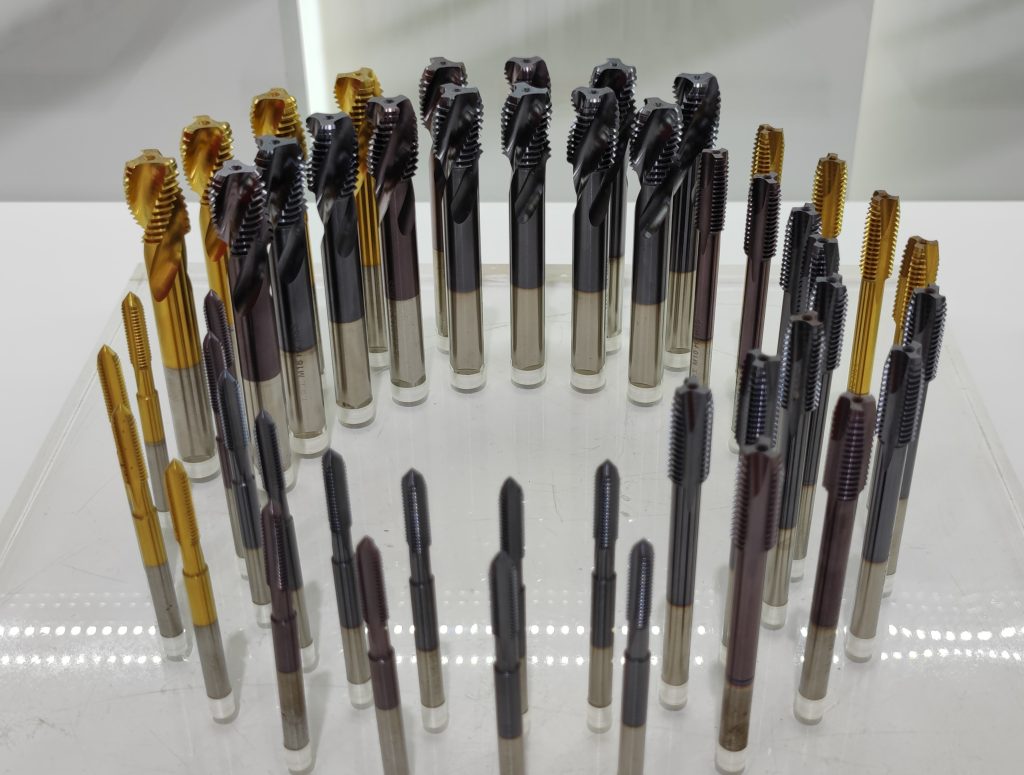